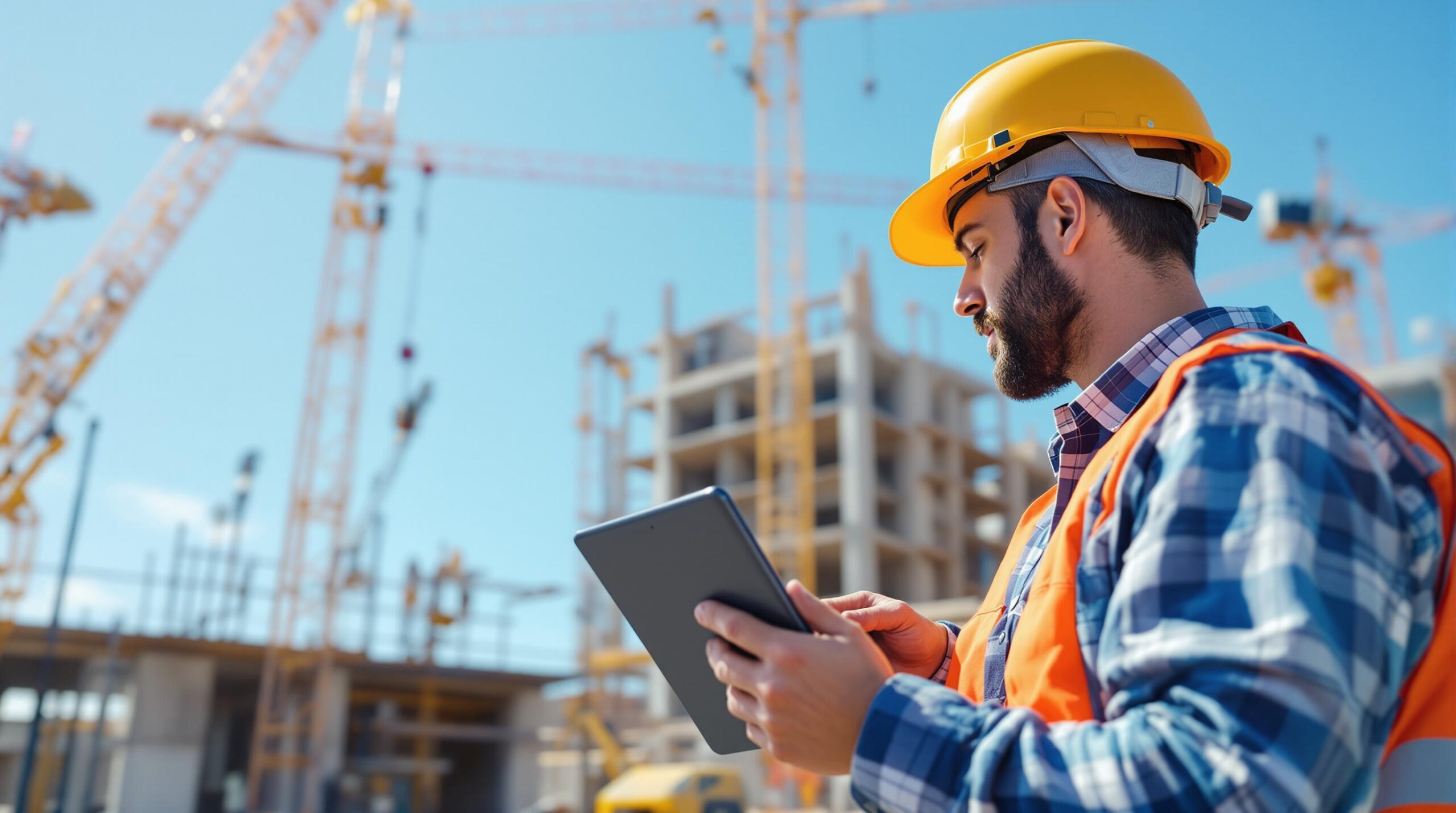
3D scanning is changing construction workflows by making tasks faster, more accurate, and cost-effective. Using LiDAR-equipped mobile devices, teams can measure sites, track progress, visualize designs, collaborate better, and reduce project costs. Here’s how:
- Accurate Site Measurements: Collect precise data in minutes, reducing manual errors.
- Progress Tracking: Compare real-time scans with project designs to spot issues early.
- Design Visualization: Create 3D models for clearer understanding and collaboration.
- Improved Collaboration: Share digital site replicas instantly, reducing site visits.
- Lower Costs: Avoid rework, optimize resources, and save on labor and travel.
3D scanning tools like SiteScape, PIX4Dcatch, and 3DR Site Scan integrate seamlessly with BIM and CAD, helping construction teams work smarter and deliver better results.
SiteScape: LiDAR 3D Scanning
The Role of 3D Scanning in Construction Apps
LiDAR-powered 3D scanning turns mobile devices into highly accurate tools for measuring construction sites down to the inch [1]. This technology eliminates the need for manual measurements, giving construction teams faster and more dependable insights.
Apps like SiteScape for iOS let teams quickly create and share virtual site models [1]. Using compatible iPhones or iPads, construction professionals can now capture, document, and analyze site data with ease.
Here’s how this technology is improving construction workflows:
- Site Documentation: Teams can generate and share detailed 3D scans of buildings and spaces in real time, which can then be used to create precise models [1].
- Project Monitoring: Tools like GeoSLAM use LiDAR and automated analytics to compare site scans with BIM models, helping teams validate progress as it happens [2][6].
- Quality Control: 3D scanning helps identify structural problems, track changes, and maintain quality throughout a project [2].
With these tools, project managers can build punch lists, address issues, and approve completed work more efficiently [3]. Additionally, apps like 3DR Site Scan integrate design files with scanned data, allowing teams to spot potential problems early [1][2].
As LiDAR-equipped devices become more common, 3D scanning is reshaping the way construction apps support critical tasks.
1. Faster and More Accurate Site Measurements
Using LiDAR-equipped mobile devices, construction teams can quickly gather precise site measurements, eliminating the need for manual methods [1]. This approach delivers highly accurate data, capturing everything from contours and dimensions to structural elements, and creates detailed digital point clouds. This level of precision is especially important during renovations, where accurate measurements directly impact bids and project estimates [1][3].
Apps like SiteScape and RoomScan Pro take advantage of LiDAR technology, allowing users to export scans in widely-used formats such as IFC, BIM, and CAD files [1][5]. With these tools, teams can document sites, produce as-built models, compare real-world conditions to design plans, and share measurements seamlessly.
Here’s a quick comparison between traditional methods and 3D scanning:
Aspect | Traditional Methods | 3D Scanning |
---|---|---|
Time Required | Hours or days | Minutes to hours |
Accuracy Level | Prone to human error | Consistent inch-level precision |
Data Capture | Limited to specific points | Comprehensive spatial data |
Documentation | Manual notes and photos | Detailed 3D models and point clouds |
Sharing Capability | Physical documents | Instant digital sharing |
By combining 3D scanning with tools like 3DR Site Scan, teams can overlay design plans onto scans. This helps identify potential issues early on and ensures measurements are spot-on [2][7].
In addition to precise measurements, 3D scanning supports real-time progress tracking, helping projects stay on schedule and within their defined scope.
2. Better Progress Tracking
3D scanning offers precise, real-time progress tracking through mobile apps. Tools like PIX4Dcatch and 3DR Site Scan let project managers compare site conditions to design plans, spot issues early, and share updates instantly using detailed digital models.
A great example is Nordkysten, which uses handheld 3D scanners to collect site data and share it immediately with stakeholders. This ensures that progress stays on track with plans. Teams can quickly identify discrepancies, compare actual conditions to designs, and provide real-time updates via mobile platforms.
When paired with project management tools, 3D scanning simplifies progress tracking. Modern construction apps use this technology to improve efficiency:
Feature | Traditional Methods | 3D Scanning-Enhanced Apps |
---|---|---|
Progress Documentation | Manual photos and notes | Detailed 3D models |
Issue Detection | Visual inspection only | Automated plan comparisons |
Stakeholder Updates | Scheduled reports | Instant access to models |
This approach is especially helpful for complex projects where older methods often fall short. Mobile apps with LiDAR capabilities can gather detailed site data without interrupting work, while cloud-based platforms ensure immediate access to the information [1][2].
sbb-itb-7af2948
3. Clearer Design Visualization
3D scanning is changing how design visualization works by creating detailed, interactive site models with LiDAR-equipped devices [1]. These models make it easier to understand designs and help construction teams interact with project plans through mobile apps.
Using LiDAR and photogrammetry, modern construction apps can produce 3D models that work seamlessly with popular design software [5]. Unlike flat 2D drawings, these 3D models allow for hands-on design reviews, automated checks for accuracy, and easy file sharing.
When combined with BIM, 3D scanning lets teams overlay design plans onto site scans. This approach helps identify and fix constructability issues early [2]. It’s especially helpful for renovation projects, where accurate documentation of existing conditions is key to getting the design right.
These 3D models also improve communication by offering clear visuals that teams can access on mobile apps [3]. They help spot and resolve design conflicts early, cutting down on delays and extra costs. With this technology, everyone involved gains a better understanding of both the design and the site’s conditions through detailed visual data.
Beyond just improving visualization, 3D scanning strengthens teamwork by providing accurate, shared site information.
4. Improved Team Collaboration
3D scanning technology is changing how construction teams work together by providing a single, reliable source of project data that can be instantly shared through mobile apps [1].
Tools like SiteScape allow teams to create virtual site replicas that can be accessed anytime on iOS devices. This reduces the need for multiple site visits and helps avoid delays in decision-making [1]. When combined with Building Information Modeling (BIM), 3D scanning lets teams track construction progress in real time by comparing laser scans to BIM models [2]. This ongoing verification ensures everyone stays on the same page regarding project status and requirements.
The digital twins generated through 3D scanning act as essential project records that teams can use throughout the construction process [4]. These detailed digital records are particularly useful for:
Aspect | Purpose |
---|---|
Verification | Ensuring work matches the original specifications |
Remote Problem-Solving | Allowing stakeholders to review and resolve issues from anywhere |
Progress Monitoring | Helping project managers track progress across multiple locations |
Documentation | Providing a comprehensive record for future use or potential claims |
Shared digital models also make it easier to plan workflows and avoid on-site conflicts [3]. This collaborative approach boosts efficiency, enabling teams to complete projects more quickly and with fewer errors.
To maximize these benefits, it’s essential to establish clear protocols for capturing and sharing 3D scan data. This ensures that all team members are working with the most up-to-date site information [1][3]. By improving communication and reducing mistakes, 3D scanning not only strengthens teamwork but also helps save on project costs.
5. Lower Project Costs
3D scanning doesn’t just improve collaboration – it also helps cut project costs by reducing errors and making better use of resources. Construction apps with this tech help avoid mistakes and streamline operations, leading to noticeable savings [1].
With automated site documentation, 3D scanning eliminates the need for manual measurements while still delivering precise results [1]. When paired with BIM, these scans offer detailed data that supports smarter planning and better cost management [2].
Here’s how the savings break down:
Cost Reduction Area | Benefit |
---|---|
Error Prevention | Spotting constructability issues early with accurate 3D models |
Efficiency Gains | Fewer site visits, quicker documentation, and smarter resource use |
Some specific ways 3D scanning impacts project costs include:
- Cutting Labor Costs: Automated processes replace time-intensive manual tasks [1].
- Lowering Travel Costs: Remote site inspections reduce the need for on-site visits [3].
- Avoiding Rework: Early detection of issues means fewer expensive fixes later [2].
- Better Resource Planning: Accurate data leads to smarter material and workforce management [5].
By turning scans into detailed BIM models, teams can make informed decisions about how to allocate resources and avoid wasteful spending [2]. Regular scanning, effective resource management, and proper training ensure projects stay cost-efficient without compromising quality.
These benefits highlight how 3D scanning is reshaping construction workflows, making projects not only more efficient but also more budget-friendly.
Conclusion
3D scanning has completely changed how construction apps are used, offering faster and more precise methods for tasks like site measurements, progress tracking, and design visualization. This technology has reshaped workflows, making them more efficient and reliable.
The advantages of using 3D scanning through mobile apps are easy to see. Tools like these excel in site measurements, ensuring design accuracy, and enabling remote inspections without sacrificing precision or dependability [1][3].
Take it from industry experts like Frank Schou Kruse from Nordkysten, who praises PIX4Dcatch for its ability to measure volumes, document sites, and seamlessly share data with clients [8]. These real-world applications showcase how this technology is making a difference.
Here’s how to get the most out of 3D scanning in construction:
Focus Area | Recommended Action |
---|---|
Technology Integration | Use LiDAR devices for detailed and accurate scans |
Workflow Optimization | Regularly include 3D scans in project records |
Team Training | Equip staff with the skills to use scanning tools effectively |
3D scanning is no longer optional – it’s a must-have for improving project results. Its ability to provide accurate measurements, track progress, visualize designs, boost collaboration, and cut costs makes it an essential tool for modern construction [1][3].
As the technology advances, its importance will only grow. Expect even greater precision, better teamwork, and more cost-effective solutions in the future [7]. By embracing 3D scanning, construction teams can work smarter, achieve better results, and stay ahead in an ever-evolving industry. </